CLIENT
FM Logistic is an international logistics corporation headquartered in France. Nestle, Wrigley, Auchan, Michelin, Volvo and more than a thousand other large companies trust her with their logistics. In Russia, FM Logistic operates 22 warehouse complexes with a total area of more than 816,000 square meters.
FM Logistic provides a full range of logistics services: from transportation and storage to the completion and delivery of B2B and B2C orders to the recipient. The services are implemented comfortably, transparently, and reliably at all stages of interaction between the company and its client.
FM LOGISTIC BUSINESS CALL
In 2019, a law on the labeling of tobacco products, perfumes, clothes, shoes, tires, photographic equipment and other groups of goods came into force. Most FM Logistic partners offer such products. The logistics company thought that its customers would be ready to outsource the routine work with marking codes, and wanted to offer this service as an additional one.
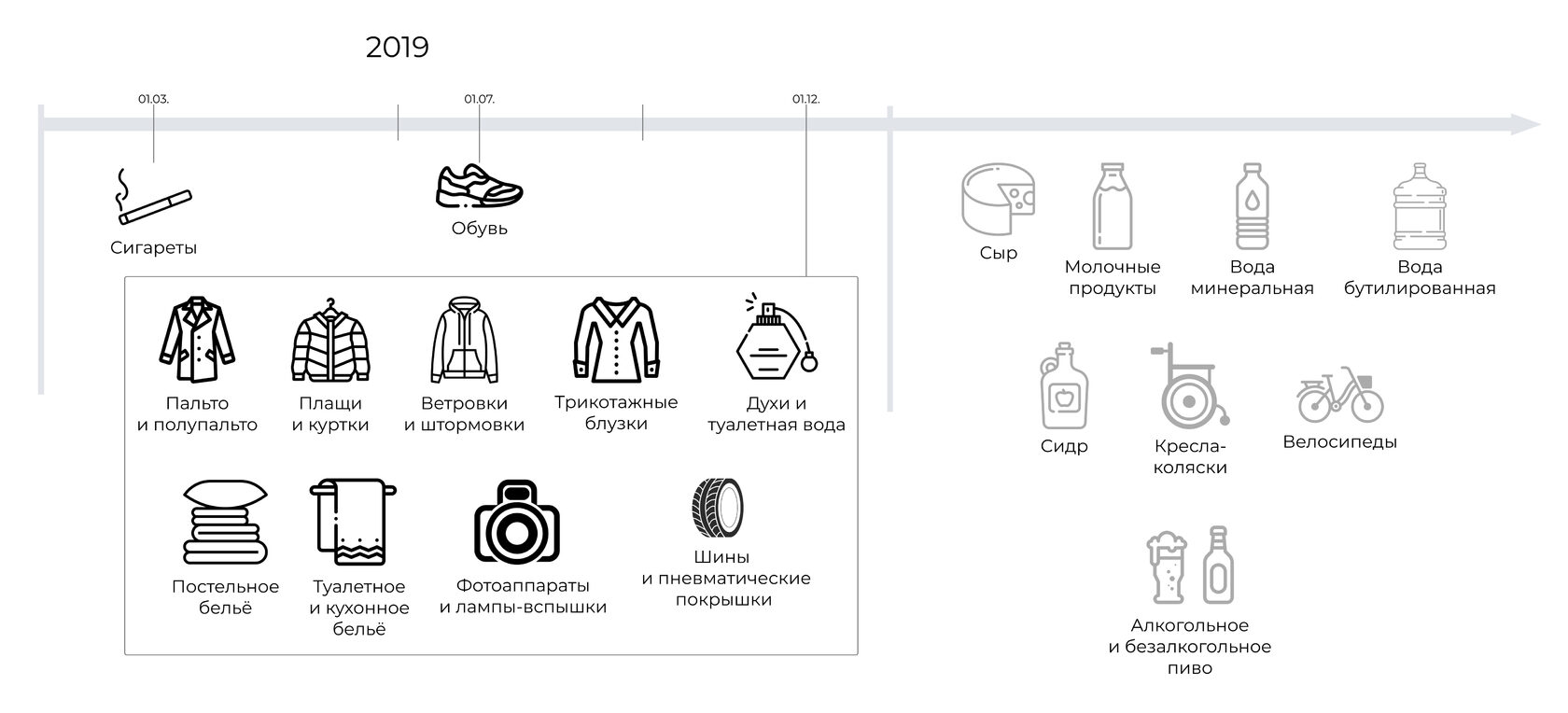
There was no ready-made solution for such a service either at the IT level or at the management level. FM Logistic's other territorial divisions also did not have experience with similar services.
It was necessary to develop all processes from scratch, and as quickly as possible: the niche was free and attractive for many companies.
In 2019, FM Logistic immediately began developing an IT labeling solution with another contractor. But after a year of work and millions in investments, she received an unstable system, each failure of which could cost FM Logistic and its partners both financial losses and criminal liability.
After that, the task was transferred to kt.team.
KT.TEAM TASK
In a short time, ensure that FM Logistic launches a service for marking goods with Chestny ZNAK codes and for tracking the movements of marked goods. The IT system that provides the service must operate 365/24/7 and be able to process tens of millions of codes simultaneously.
LABELING IS NOT JUST ABOUT STICKING A STICKER
The law on product labeling was adopted in order to ensure the transparency of commodity markets and reduce the number of counterfeit goods. Therefore, the product to be labeled should not only be “marked” with a code immediately after production or crossing the border, but also track its path from the manufacturer to the end customer and transfer the data on each stage of the goods movement to the regulatory authorities.
The life cycle of a labeled product consists of five major stages, each of which involves several business processes with branches and restrictions. The owner must report every change in the status of the goods to Chestny ZNAK.
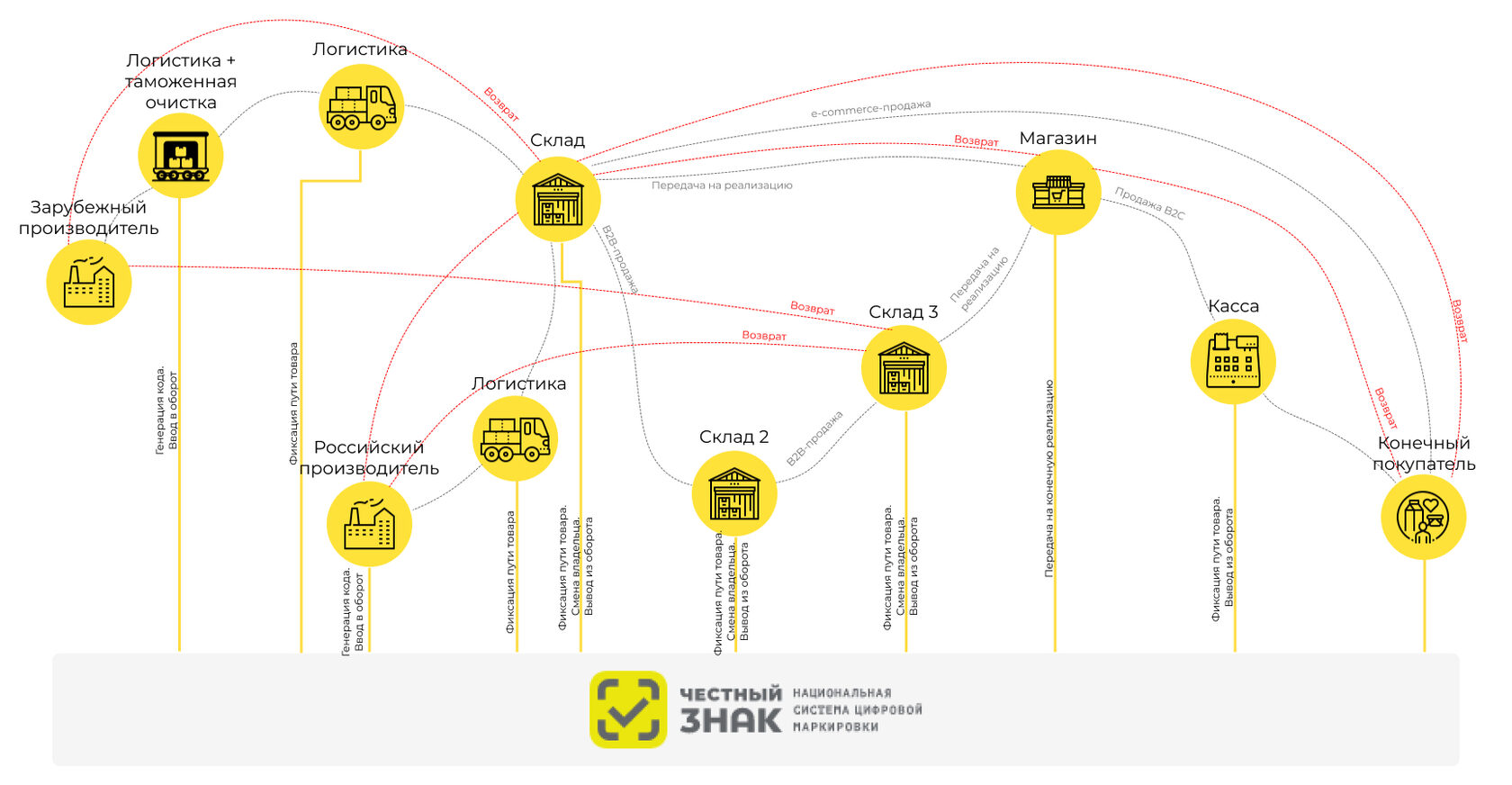
In addition, labeled goods also move within FM Logistic's own business processes.
Our team:
- visited FM Logistic warehouses twice;
- spent hundreds of hours of calling FM Logistic employees from warehouse workers to line managers;
- analyzed the legislation on labeling;
- studied the main business process and dozens of invested processes in which labeled goods are involved;
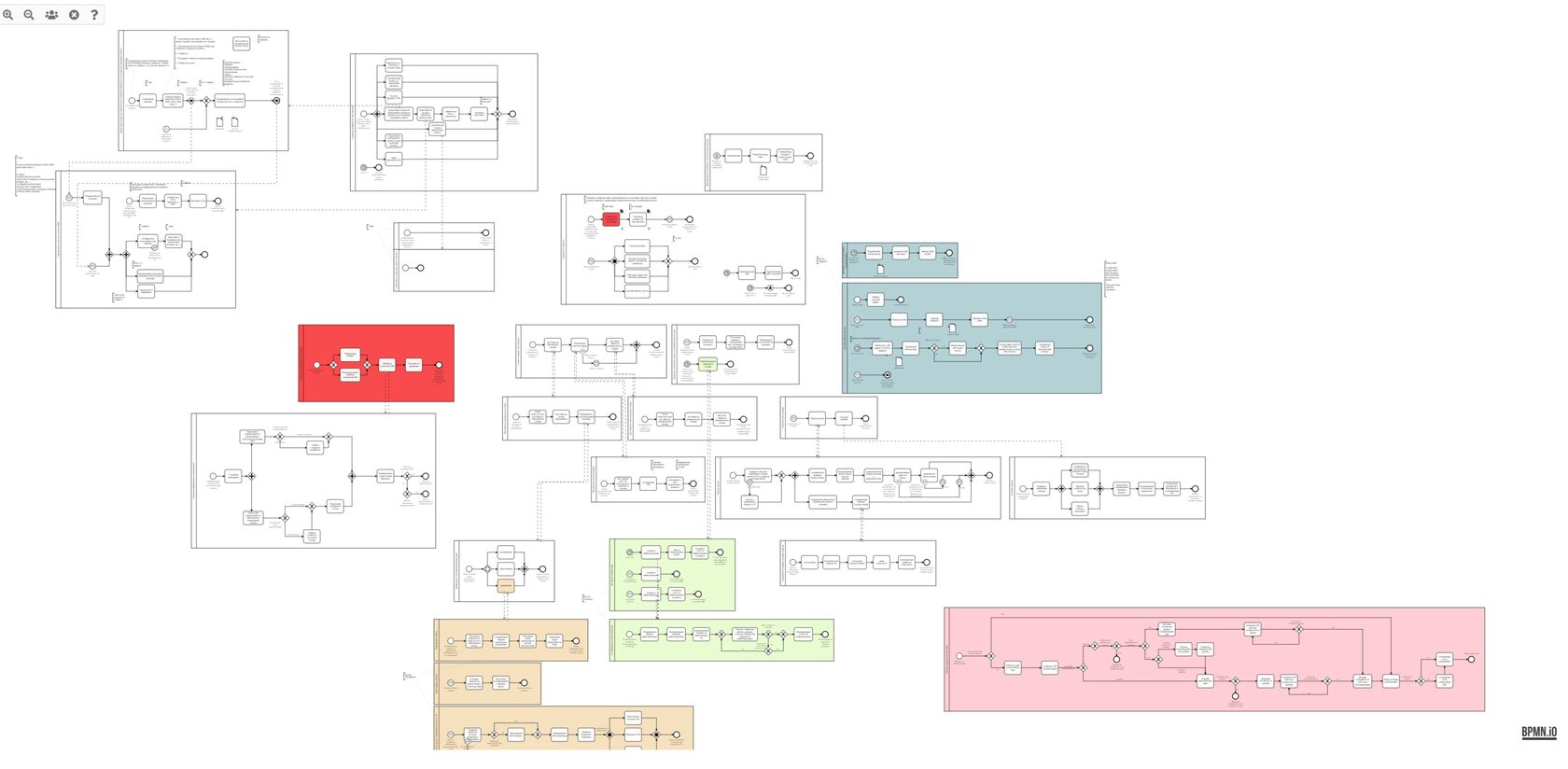
- understood the operation of the “Chestny ZNAK” system;
before you start working on the code.
This allowed us to avoid the previous contractor's mistake. Instead of taking the existing warehouse scanner application and “finishing” it (this is the path our colleagues chose), we developed a microservice system from scratch. The product was named ParaDigma.
RESULT 1. THE SERVICE OF OBTAINING CODES FROM THE “CHESTNY ZNAK” SYSTEM REQUIRES FM LOGISTIC TO HAVE MINIMAL ADDITIONAL STAFF COSTS
We have fully automated the process of obtaining Honest Mark codes. FM Logistic employees perform only the incoming operation of uploading documents and the final operation of gluing codes to product packages.
ParaDigma analyzes downloaded invoices and searches them for items to be labeled. Eliminates invoices that do not have such items. In invoices that contain such items, ParaDigma highlights their type and quantity, and then automatically requests codes from Honestny ZNAK. Codes uploaded to Paradigma are automatically linked to the item name.
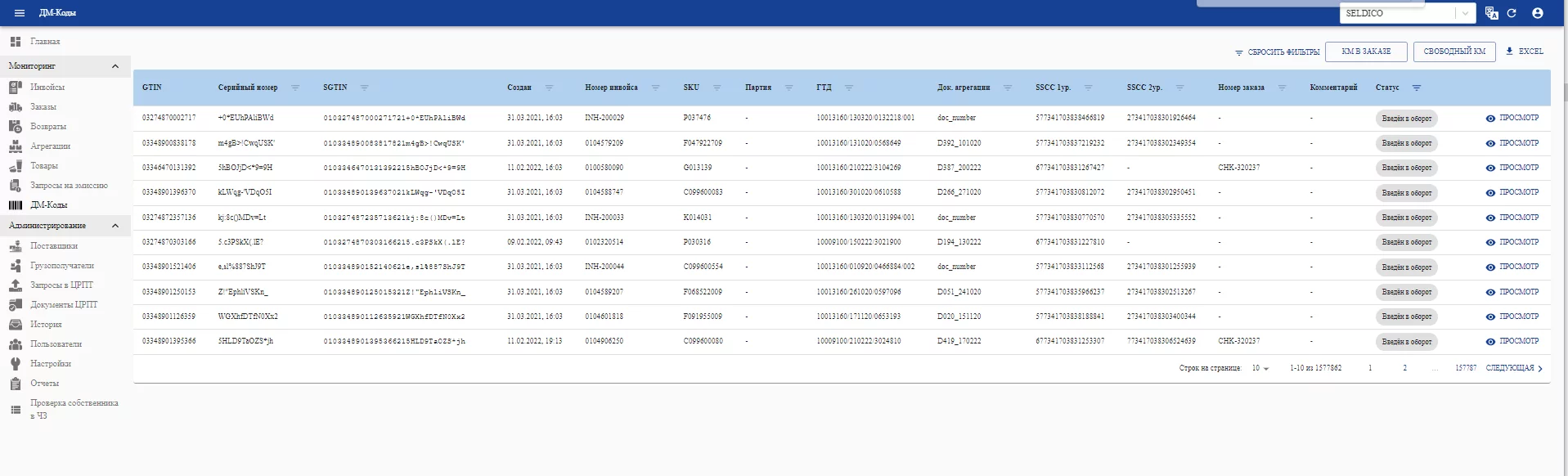
Employees receive a ready-made list of codes of the right type and in the right quantity. All that remains is to print and paste them.
RESULT 2. MOVEMENTS OF GOODS FROM RECEIPT TO WITHDRAWAL FROM CIRCULATION ARE AUTOMATICALLY RECORDED IN AN “HONEST SIGN”
The marking code is scanned during any transaction with the product. This may be inventory of a warehouse, movement within a warehouse, wholesale, sale to the end consumer, return, inclusion in a consolidated cargo or set, etc.
Depending on the type of operation, ParaDigma performs a set of actions that ensure the transfer of data to the “Chestny ZNAK” system: it searches for the code within its database, checks its current status, checks its current status, checks the new owner and the previous owner, makes a request to change the status or transfers data about the stage of cargo processing.
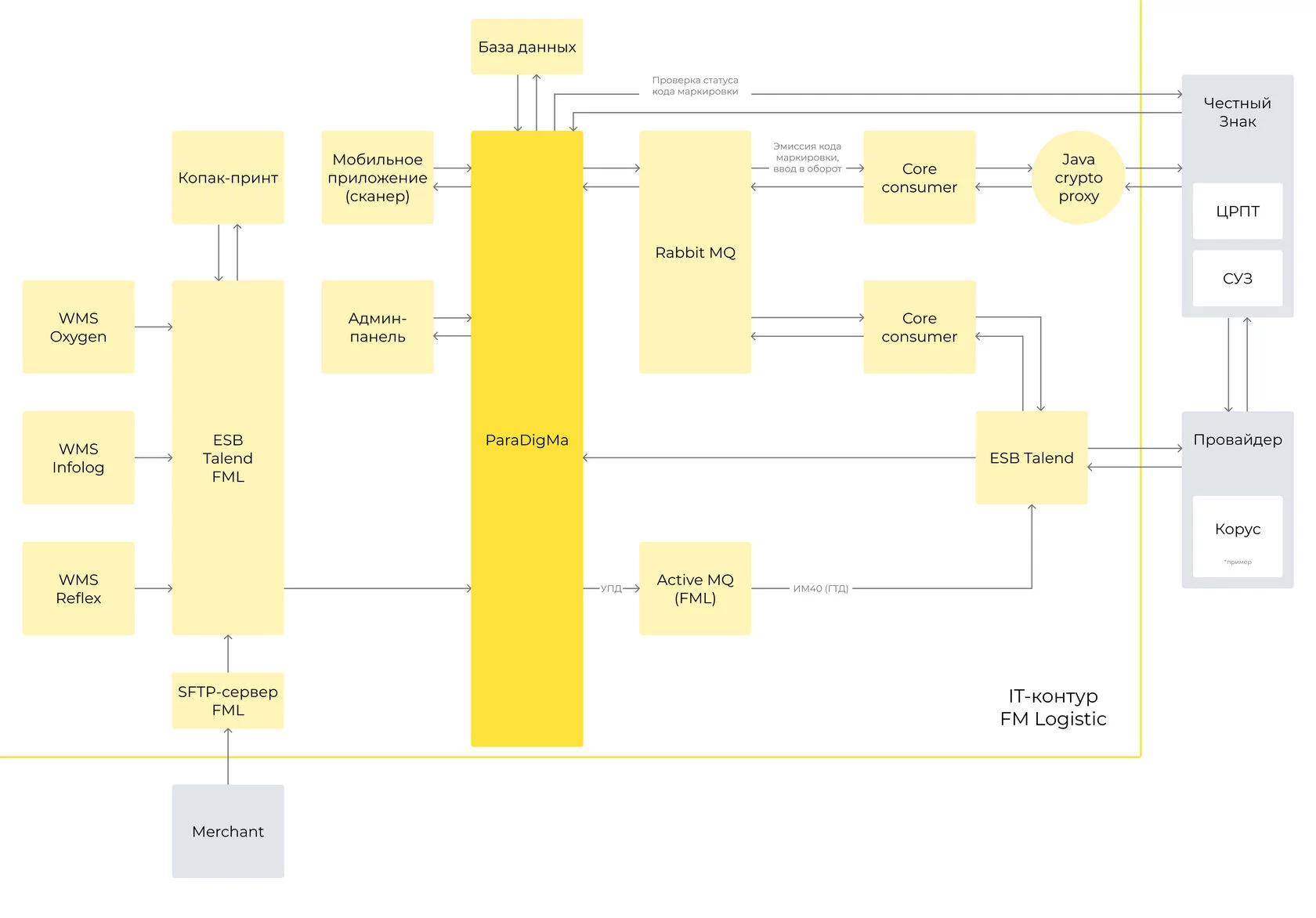
Thus, FM Logistic helps customers comply with legal requirements at no extra cost for both their own staff and IT.
RESULT 3. FM LOGISTIC CLIENTS CAN CHOOSE WHETHER THEY NEED THE WHOLE SERVICE OR ONLY PART OF IT
The product labeling and tracking service consists of a group of microservices, each of which has its own area of application.
These microservices are interconnected, but they can also work separately.
For example, an FM Logistic customer entrusts labeling to another provider or handles it himself. But if he wishes, he can upload codes to Paradigma and entrust FM Logistic to further track goods and transfer information to Chestny ZNAK. Optional — either only for moving around the warehouse, or until the goods are withdrawn from circulation.
RESUME
The ParaDigma perfume labeling service was launched in 5 months in MVP mode (August 2020 — January 2021), and fully deployed in 8 months (April 2021).
The system consists of microservices. It has 20 million lines of code in its core. By comparison, the space shuttle is operated by 400,000 lines of code
In 2021, ParaDigma received codes for 25.72 million items.
The Paradigma product labeling and tracking service is fully used by 6 FM Logistic partners, including Shiseido and Chanel.
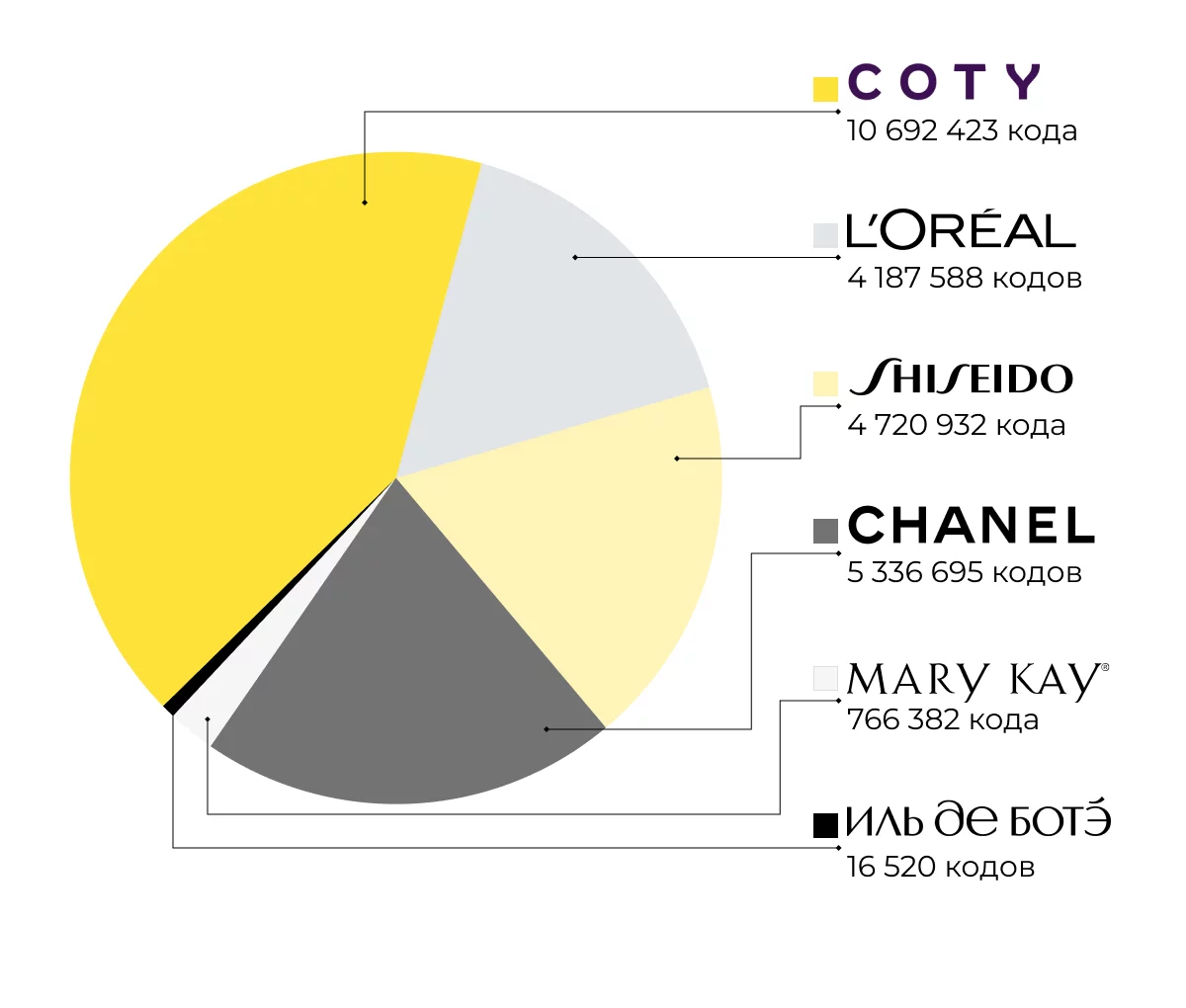
Two more FM Logistic partners issue codes through another service, but while goods are in the ecosystem, FM Logistic uses ParaDigma to track the movement of goods.
ParaDigma operates 365/24 and does not require a shutdown to perform the service.
At the same time, ParaDigma employs up to 300 FM Logistic employees. At the same time, the system receives data from the client's three WMS systems and exchanges data with the Chestny Znak system and alternative labeling service providers.
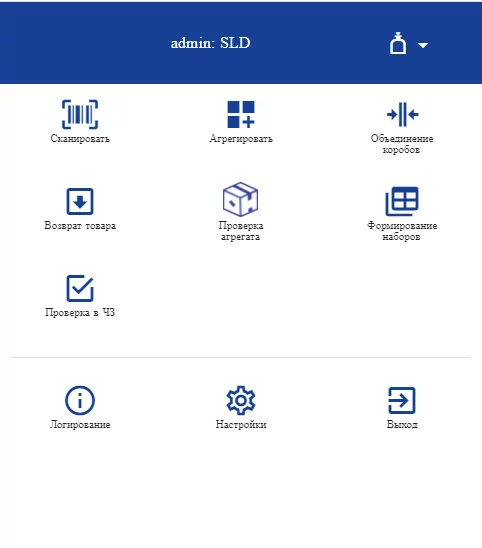
In April 2022, we added labeling for additional product groups: footwear products, clothing items; bed linen, table linen, toilet linen and kitchen linen. With minimal improvements, we are ready to connect the product groups “new pneumatic rubber tires and tires”, “cameras, flash lamps and flash lamps”, “bicycles and bicycle frames”, “wheelchairs”, “packed water”, and “dietary supplements”.
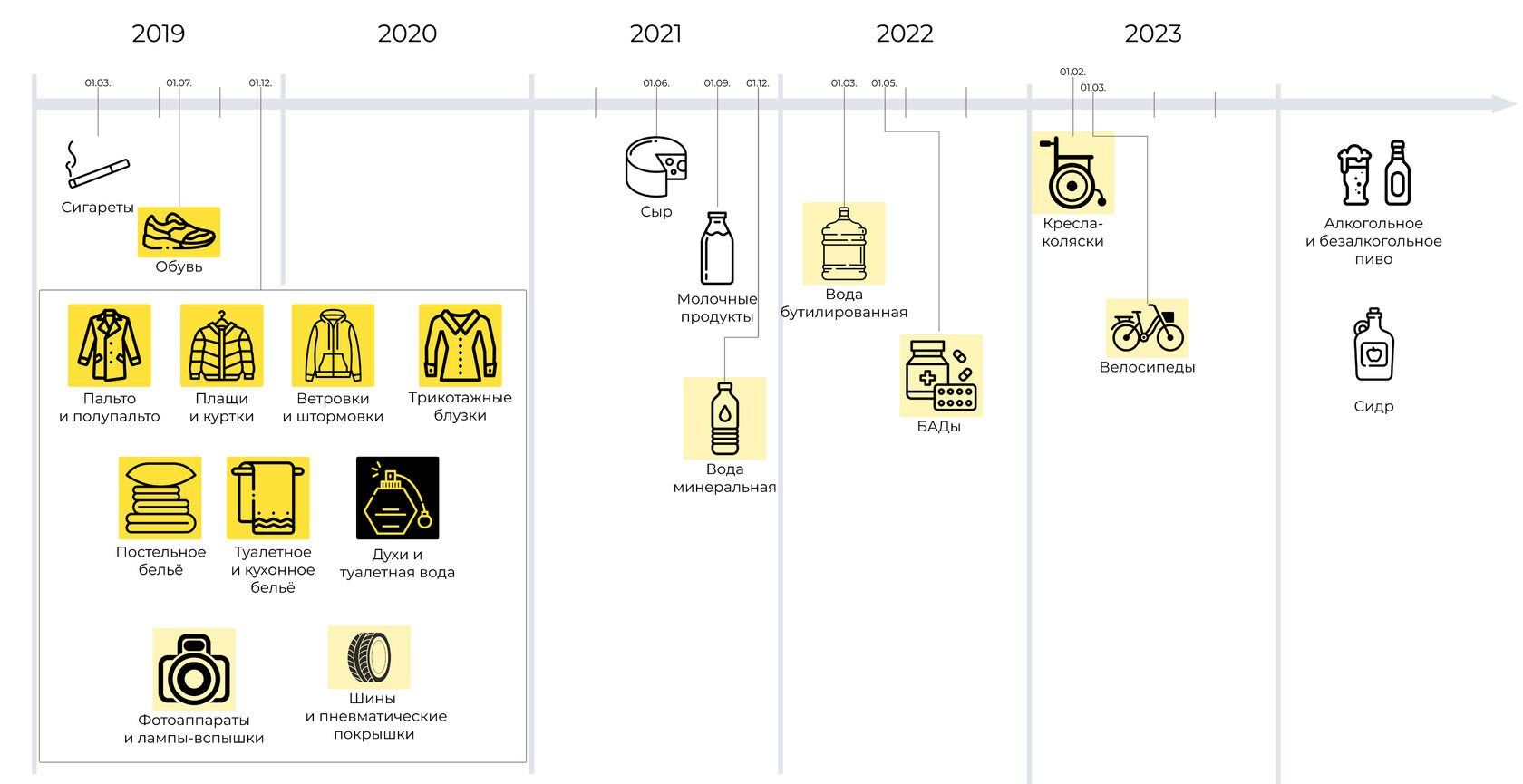