Client
FM Logistic is an international logistics corporation headquartered in France. Nestle, Wrigley, Auchan, Michelin, Volvo and more than a thousand other large companies trust her with their logistics. In Russia, FM Logistic operates 22 warehouse complexes with a total area of more than 816,000 square meters.
FM Logistic provides a full range of logistics services: from transportation and storage to the completion and delivery of B2B and B2C orders to the recipient. In addition, the company provides its customers with additional services: customs clearance of goods, labeling, etc.
Business goal
To provide FM Logistic customers with a full range of logistics services in a comfortable, transparent and reliable manner at all stages of interaction.
Client problem:
Each warehouse has 3,000 people working on inventories every day, and yet the data becomes out of date before reports appear in the system
FM Logistic has thousands of partners: Leroy Merlin, Michelin, Auchan... Tens of millions of SKUs are in stock every day. Hundreds of heavy trucks are unloaded and loaded. The goods are moved inside the warehouse. On the territory of FM Logistic, they pack B2B and B2C orders from customers, form joint deliveries, packages, and issue returns. Items are about to expire.
As a result, the actual availability and quantity of goods may not be the same as planned. Since FM Logistic is financially (and in some cases even criminal) responsible for goods in stock, the company must promptly and reliably inform customers about the condition and quantity of their items in stock.
But even when FM Logistic's 3,000 employees were taking inventory in the “traditional” way (all procedures were manual), warehouse reports became out of date faster than they reached customers.
FM Logistic has set us the task of providing conditions for timely, complete and high-quality inventory, while reducing inventory costs.
Features of inventory in a warehouse with dozens of merchants
The inventory process has many nuances:
- Where is the inventory taken: at a specific warehouse location? In the entire merchant zone? All in stock?
- What is the purpose of inventory: checking the availability of goods? the amount of leftovers? writing off goods that have passed the expiration date? et al.
- Why is inventory taking place? Is it a regular routine procedure or is there a special reason for carrying it out?
- Where should the results be?
- What should I do with the surplus?
- What if the product code is duplicated?
- What to do about overgrading?
There are hundreds of such questions, and they concern 35 of the company's business processes. Without a practical understanding of inventory, it is easy to forget about them. As a result, an IT solution based on theoretical knowledge will be useless.
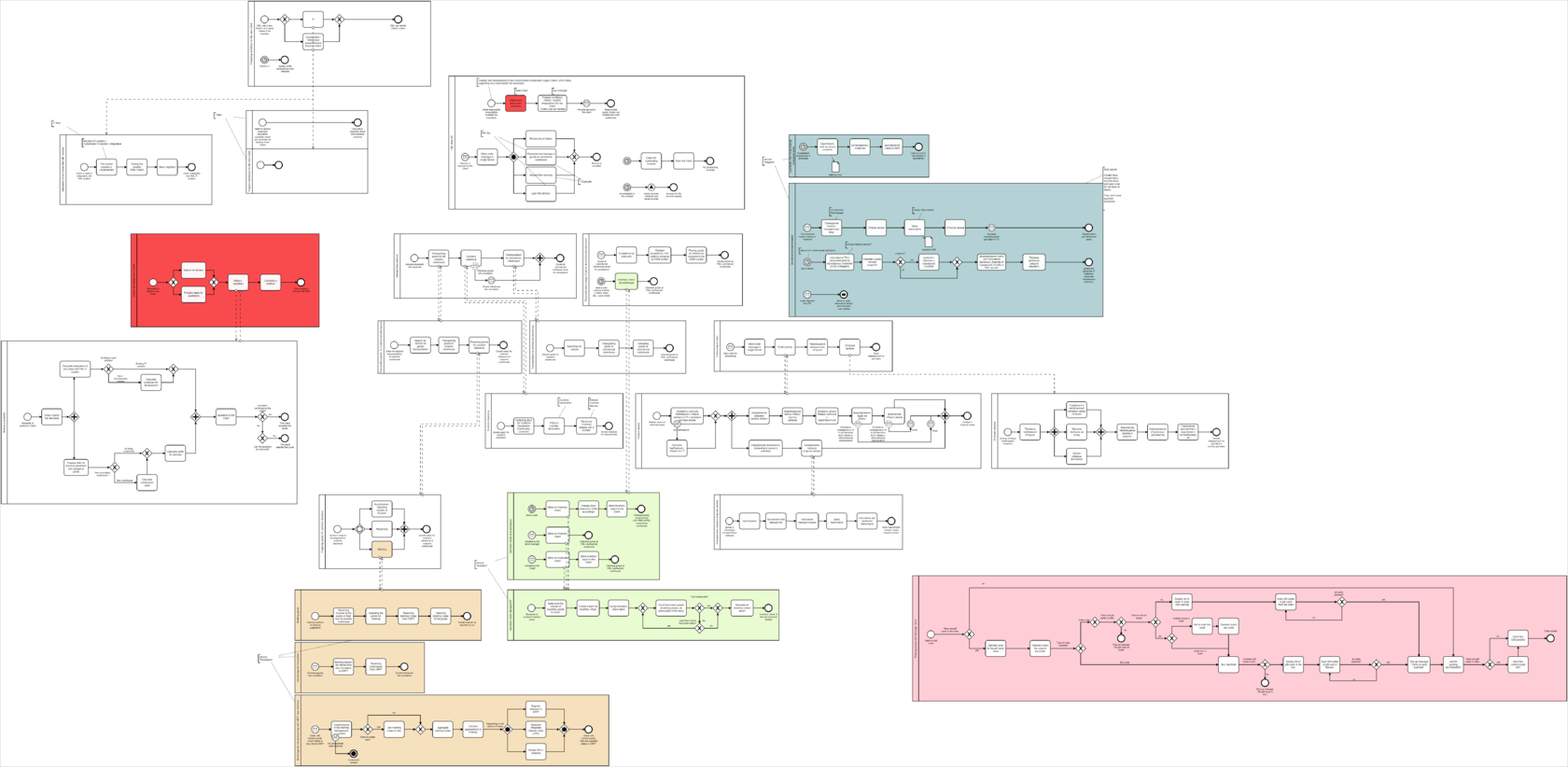
Prior to development, the kt.team team made hundreds of calls with employees “on the ground” and twice visited FM Logistic warehouses to study the process in detail.
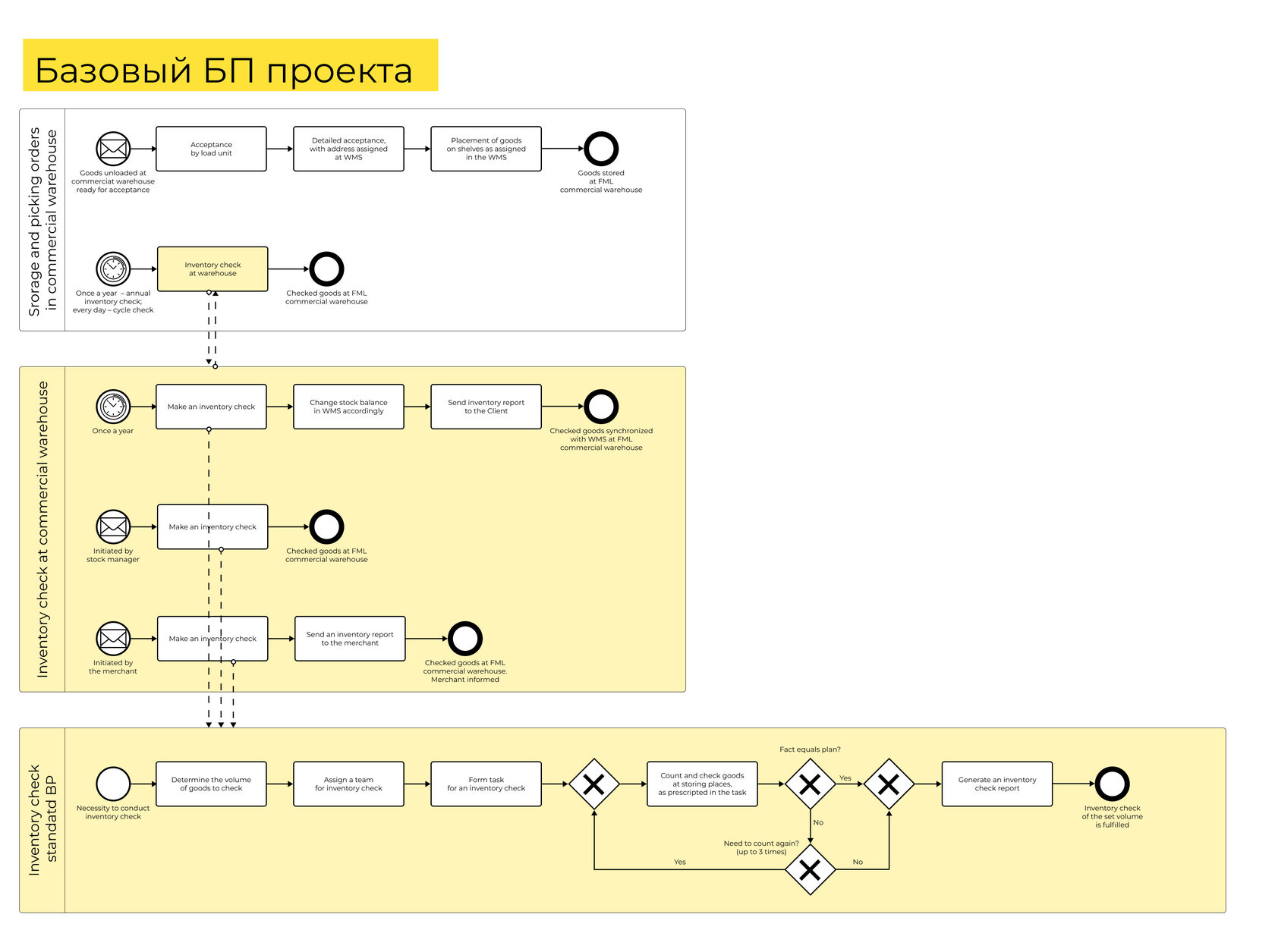
Solution: sticking all goods + automated inventory system in warehouses
Stickers allow you to get information about the cargo without searching and reconciling
All goods stored in FM Logistic warehouses are marked with stickers. Stickers refer to cargo records in the company's systems: data about the cargo owner, container contents, storage location, number of items, etc.
Previously, the warehouse inventory procedure was structured as follows.
- The employee received a task to inventory a warehouse or a list of goods.
- Using a scanner, he read codes, and the data from them was entered into a text file.
- I manually recalculated the number of items and supplemented the information in a text file.
- Then he compared the inventory results with the task.
- If resorted, he had to return to his workplace, search the systems where there should actually be “extra” cargo, then return to the warehouse and ship this cargo to the</aside> right address.
Inventory applications make the procedure faster, easier and more accurate
We have developed three inventory applications for warehouse and accounting scanners.
Now, after receiving an inventory task, an employee works with only one source of information — a scanner. On the screen, he sees the storage location that requires verification, and, if necessary, the exact quantity of goods, batch number, shelf life, and other inventory data.
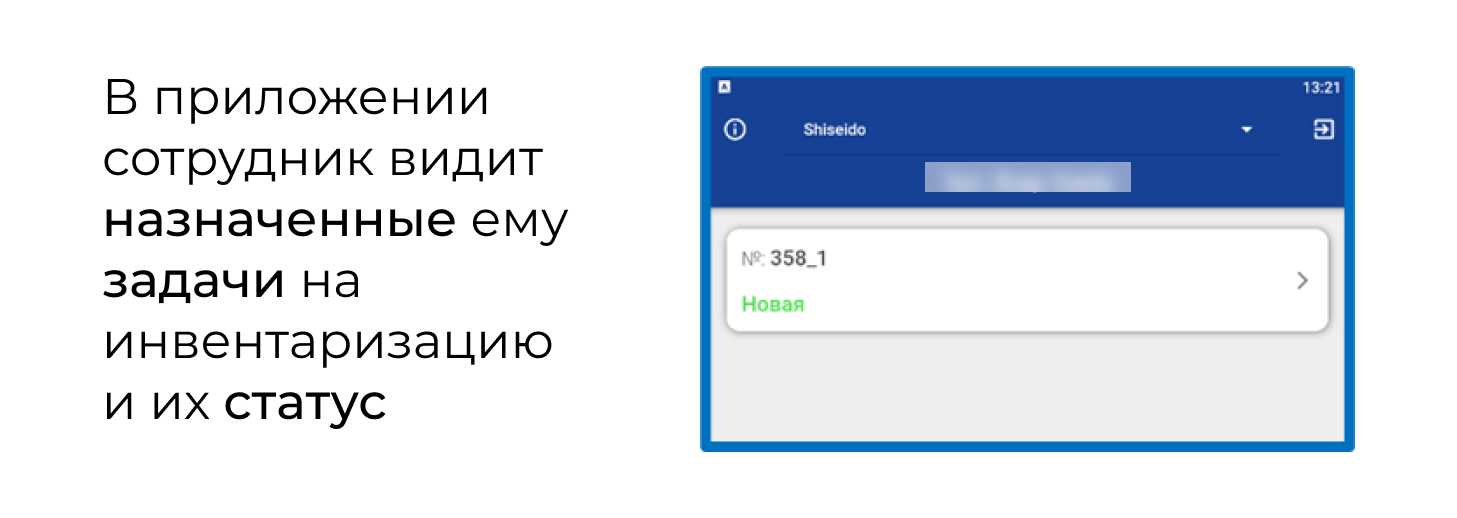
The scanner will also inform the employee if the marking code is duplicated for several items or is mechanically damaged and requires re-sticking.
If the inventory plan does not match the fact, the system will inform the line manager about this and he will be able to schedule a recalculation of the goods. Based on the results of the inventory, the line manager receives an automatically generated report on the goods actually in the audited place.
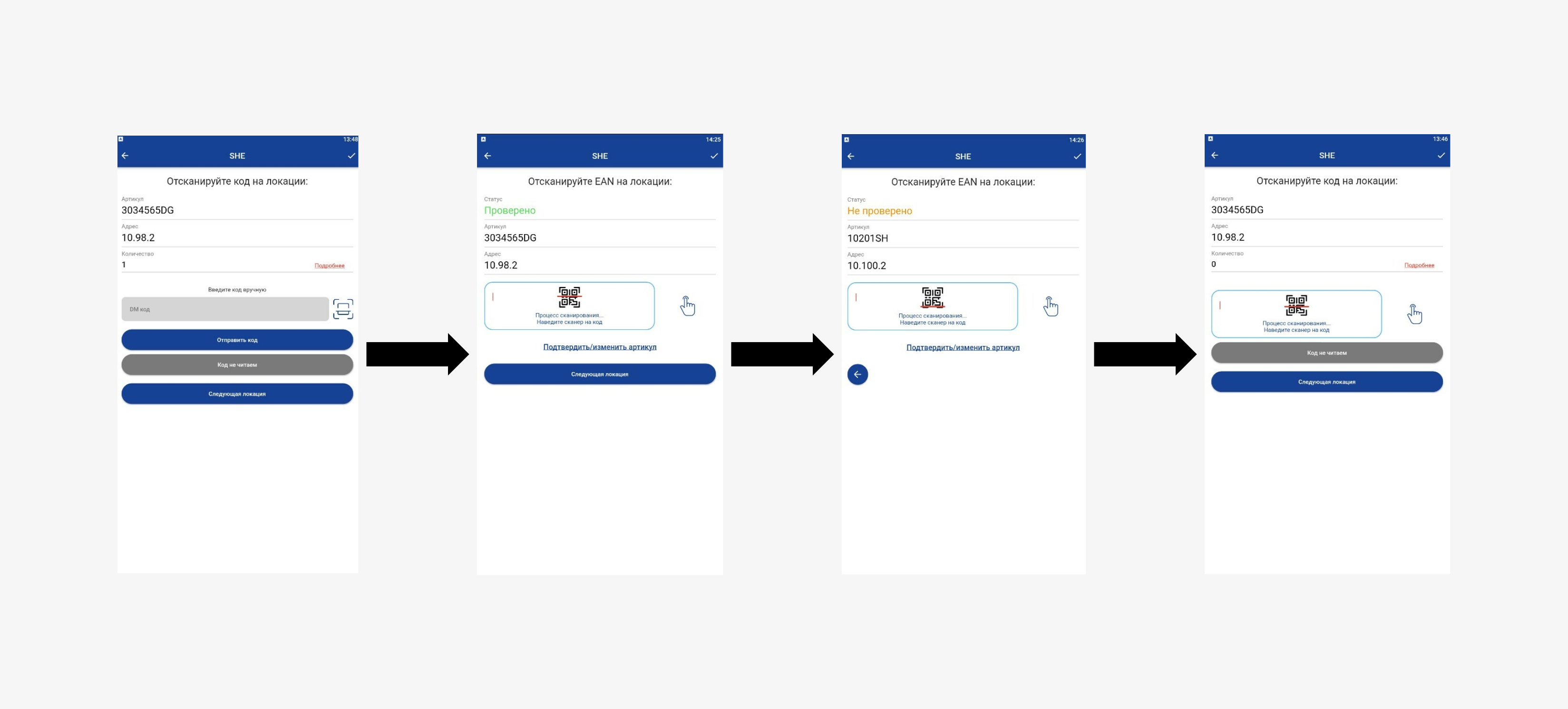
If an employee finds an unplanned item at the warehouse, the scanner will notify you with a sound signal. The employee immediately puts such goods in the “anomaly zone” in order to later move them to the correct storage location. Thus, it is possible not only to detect overstock, but also to restore order in the warehouse at a lower cost.
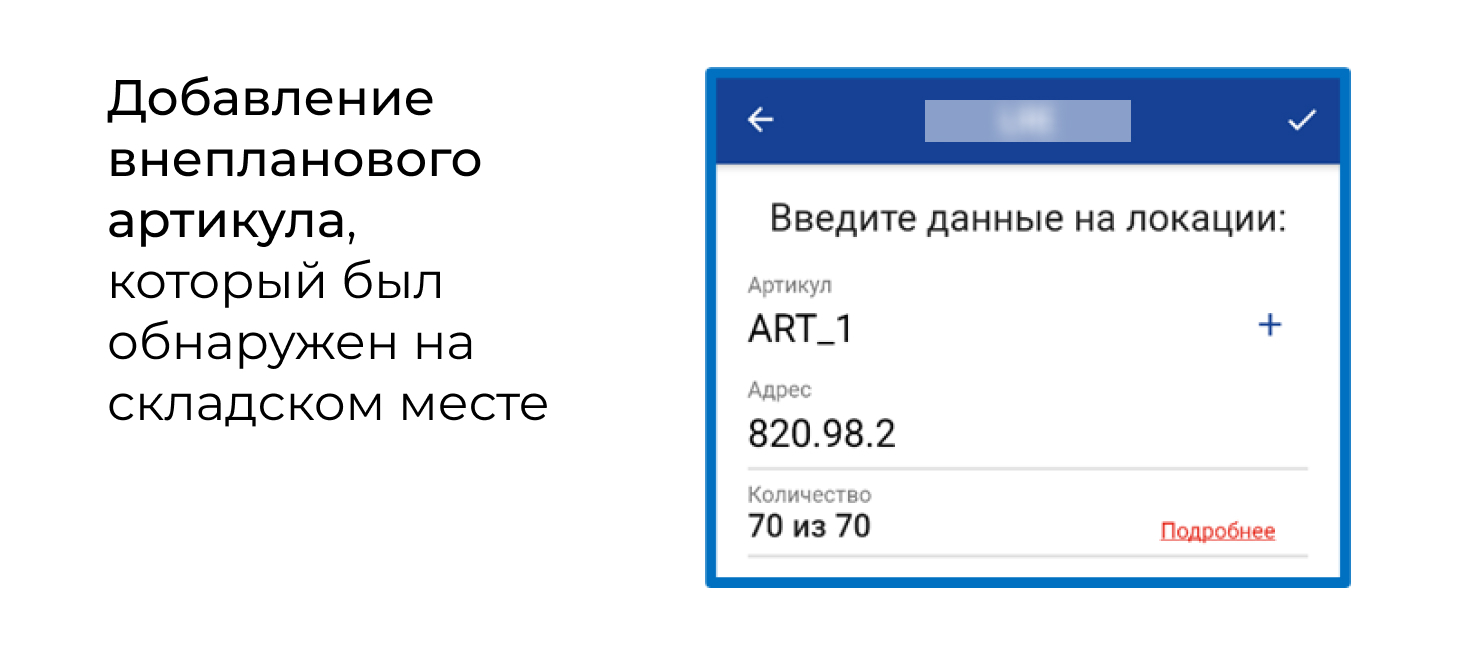
The scanner will also inform the employee if the marking code is duplicated for several items or is mechanically damaged and requires re-sticking.
If the inventory plan does not match the fact, the system will inform the line manager about this and he will be able to schedule a recalculation of the goods. Based on the results of the inventory, the line manager receives an automatically generated report on the goods actually in the audited place.
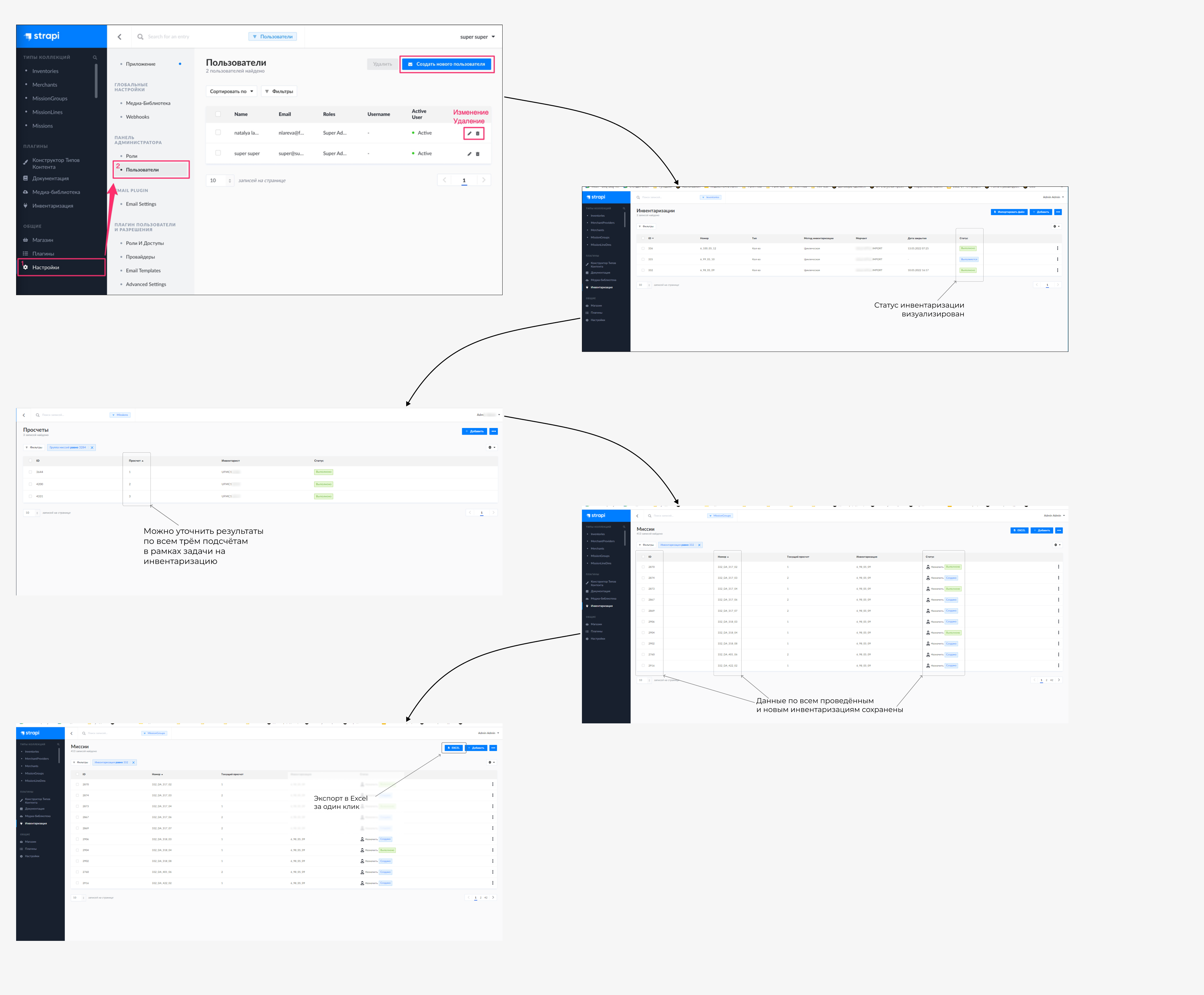
The report to the client is generated automatically in the administrative application.
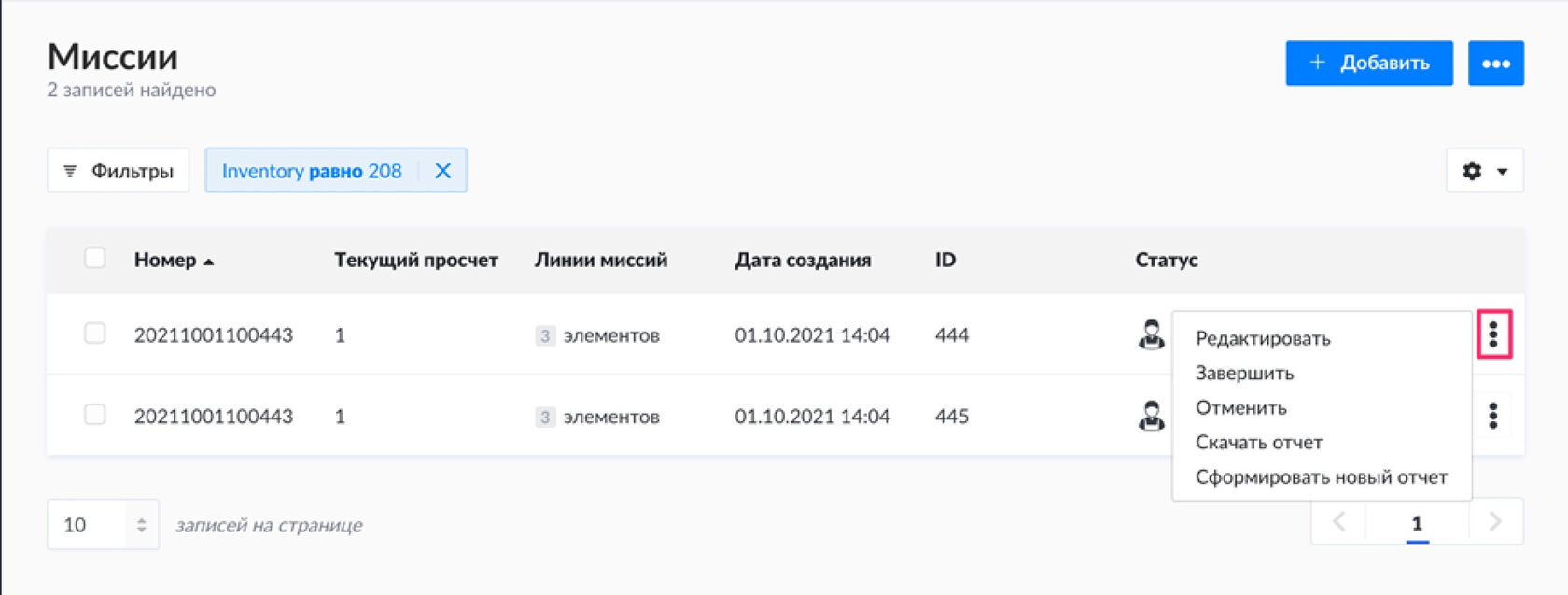
results
- Inventory labor costs and costs have been reduced threefold.
- It is possible to conduct both cyclical inventories and full inventories rhythmically.
- Recorting is detected more quickly and returned to the right place.
- Reporting on storage services for merchants is generated automatically and is becoming more accurate.
- A report can be sent to a merchant in one click immediately after the inventory is completed.
- Corporate reporting is becoming more reliable.
- The company receives an additional source of information for making management decisions.